Every Shape Your Shop Produces
- Beams
- Channels
- Angle Iron
- HSS – Square & Rectangular
- Flat Bar & Strip Plate
- Stair Stringers
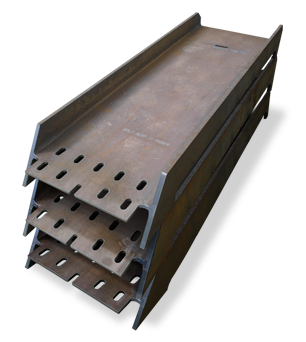
PythonX STRUCTURAL Nearly Eliminates Material Handling
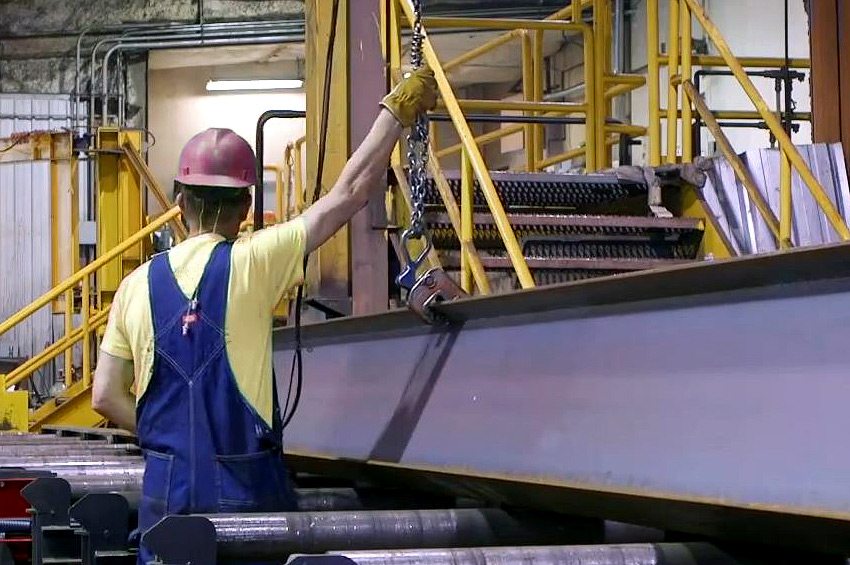
Our competitors’ solution? Sell you conveyors and transfers to make material handling less difficult.
Our solution? Eliminate the need for material handling. PythonX STRUCTURAL eliminates up to 80% of the lifting, flipping and shuttling of pieces between work centers that you are probably doing now. With PythonX STRUCTURAL, time and labor goes into fabricating steel, not moving it around your shop.
You Draw It, PythonX STRUCTURAL Cuts It
- Bolt Holes – Best in class cut quality, AISC/EN1090 compliant, in unlimited sizes with no tool changeovers
- Copes – with CNC machine accuracy
- Cut To Length – 6 times faster than Band Saw
- Miter Cuts – with compound angles
- Notches & Cutouts – including large cutouts
- Slots – for knife connections and bracing
- Stair Stringers – including layouts for treads
- Weld Prep Bevel Angles
- Scribing & Marking – all letters and numbers
- T-Beams – from splitting I-Beams
- Layout Marks – for clips and stiffeners
Watch PythonX Cut Quality In Action In The Videos Below!
Only Available on PythonX STRUCTURAL – Patented Bolt Hole Process
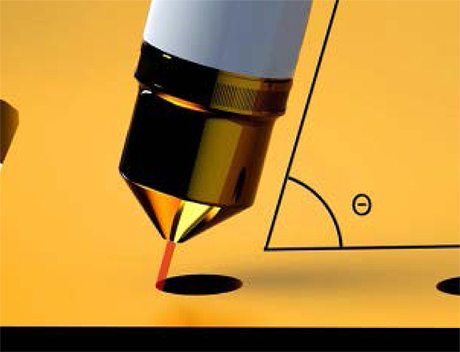
PythonX STRUCTURAL tilts the torch, instantaneously changes speeds and uses sophisticated software to produce straight through holes that are NEARLY TAPERLESS.
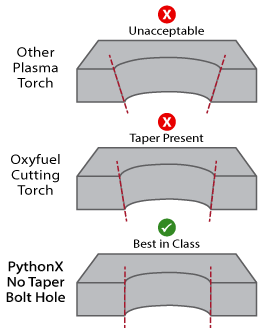
Material Sizes for Processing
PythonX STRUCTURAL fabricates a much wider variety of structural sections and sizes compared to conventional single-purpose machines. Whether it’s a 2″x2″ angle or a large W36x300 beam, and everything in between, PythonX STRUCTURAL automatically processes 99% of the typical structural fabrication shop’s material.
And PythonX STRUCTURAL parts are more accurate than parts from traditional fabrication equipment or manual fabrication:
- The measuring cart system works with the robot to locate features exactly according to part drawings.
- Everything is done in one pass, rather than multiple stations, so all holes and features are placed more accurately relative to each other.
Profile Shape | Minimum | Maximum |
---|---|---|
Beam Width | 4 in. (101 mm) | 48 in. (1219 mm)** |
Beam Height | 4 in. (101 mm) | 18 in. (457 mm) |
HSS Width | 2 in. (51 mm) | 12 in. (308 mm) |
HSS Height | 1 in. (25 mm) | 18 in. (457 mm) |
Channel Width | 3 in. (76 mm) | 36 in. (914 mm) |
Channel Height | 1 in. (25 mm) | 4 in. (101 mm) |
Angle Width | 2 in. (51 mm) | 10 in. (254 mm) |
Angle Height | 2 in. (51 mm) | 10 in. (254 mm) |
Strip/Plate Width | 4 in. (101 mm) | 36 in. (914 mm) |
Strip/Plate Thickness | 0.25 in. (6.3mm) | 1.25 in. (32 mm) |
Part Length | Standard system accommodates 40 ft. (12 m) lengths. Can increase to 80 ft. (24m) in increments of 4 ft. (1.2m). |
|
Material Thickness | Pierce up to 1.50 in. (38 mm).
Edge Start up to 2 in. (51 mm). Can upgrade to 2 in. (51mm) pierce, 3 in. (75mm) edge. |
Profile Shape | Minimum | Maximum |
Beam Width | 4" (101 mm) | 48" (1219 mm)** |
Beam Height | 4" (101 mm) | 18" (457 mm) |
HSS Width | 2" (51 mm) | 12" (308 mm) |
HSS Height | 1" (25 mm) | 18" (457 mm) |
Channel Width | 3" (76 mm) | 36" (914 mm) |
Channel Height | 1" (25 mm) | 4" (101 mm) |
Angle Width | 2" (51 mm) | 10" (254 mm) |
Angle Height | 2" (51 mm) | 10" (254 mm) |
Strip/Plate Width | 4" (101 mm) | 36" (914 mm) |
Strip/Plate Thickness | 0.25" (6.3mm) | 1.25" (32 mm) |
Part Length | Standard system accommodates 40 ft. (12 m) lengths. Can increase to 80 ft. (24m) in increments of 4 ft. (1.2m). |
|
Material Thickness | Pierce up to 1.50" (38 mm).
Edge Start up to 2" (51 mm). Can upgrade to 2" (51mm) pierce, 3" (75mm) edge. |
How Long To Fabricate This Beam In Your Shop ?
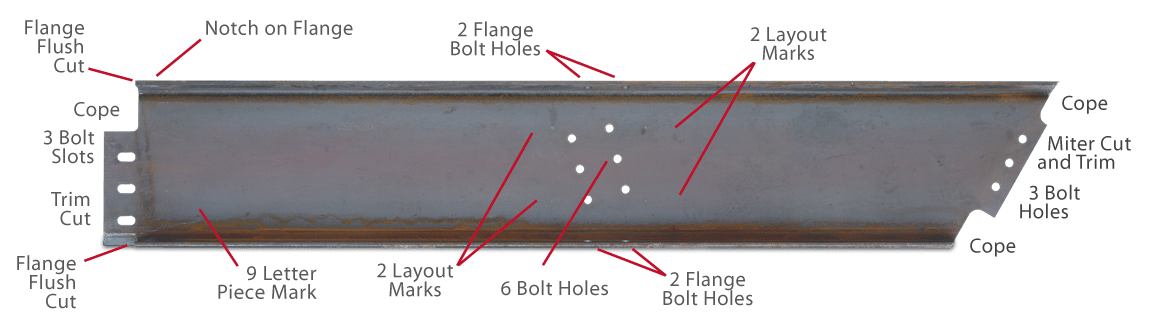
Minutes for PythonX STRUCTURAL
Minutes for CNC Beam Drill Line With Bandsaw
Minutes for All Manual Fabrication Shop
There are 40 distinct cuts and features made to produce this beam. Think how many people and machines are needed to get that done with traditional fabrication equipment. Think of the cost.
With PythonX STRUCTURAL there’s no layout work, no programming the cuts, no tool change . . . really no operator involvement, except to make sure the right beam was loaded on the infeed conveyor and to push “START.”
And how much material handling was involved with processing this beam on the PythonX STRUCTURAL? Two steps: load the raw beam and remove the finished beam. That takes two minutes total. A manual shop would need about 30 minutes to lift, flip and move the beam around, each movement increasing risk of a handling accident. Shops with ‘conventional’ fab automation still need about 20 minutes to move the piece from one machine to another, over to a workbench for coping and torch cutting – it adds up.
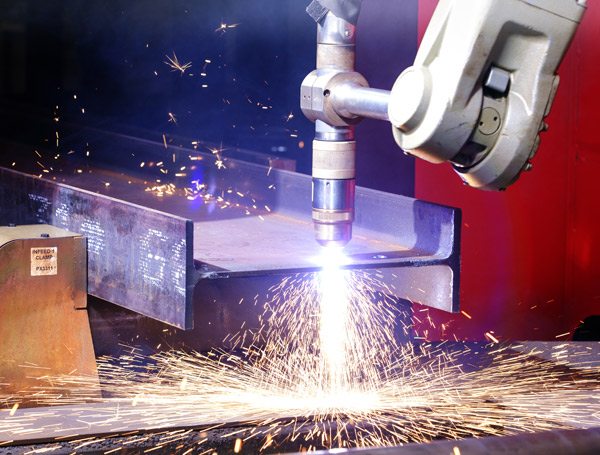